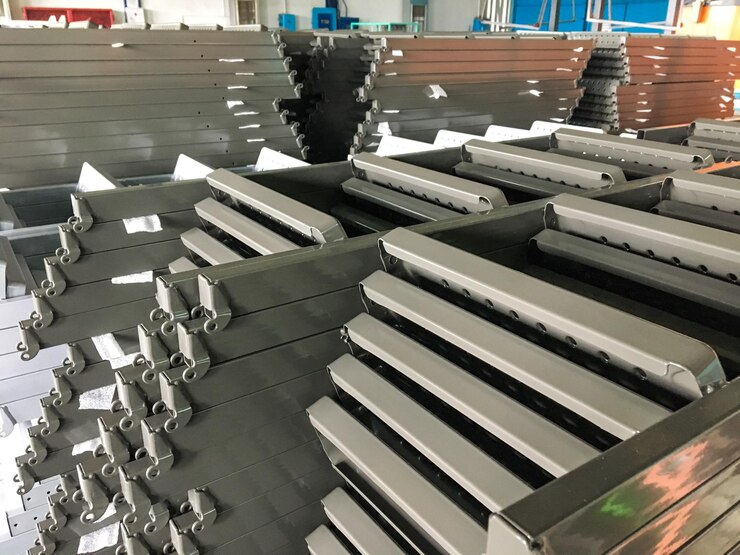
5 Key Steps in the Galvanizing Process You Should Know
Galvanizing is a widely used approach within the industry worldwide to defend metals, mainly metallic, from corrosion. It gives a prolonged-lasting, lengthy-lasting coating that guarantees structural integrity and extends the lifespan of metal additives. Understanding this method is critical for industries that depend upon metallic protection. Below, we spoil down the 5 key steps inside its technique, detailing how everyone contributes to the effectiveness of this approach.
Surface Preparation
The first and maximum important step in the galvanizing device is surface education. This ensures that the metallic is easy and loose from impurities, allowing the zinc coating to stick well. Surface contaminants which encompass dust, grease, and rust can intervene with the coating system, primarily to terrible adhesion and decreased safety in competition to corrosion.
This step consists of numerous levels, beginning with degreasing or cleansing. A chemical answer is used to do away with oil, grease, and specific natural residues from the floor. Next comes pickling, in which the metal is submerged in an acid tub to take away rust and mill scale. Finally, the floor undergoes fluxing, which entails dipping the metal in a zinc ammonium chloride solution. Fluxing prevents oxidation earlier than the steel is immersed in molten zinc.
Surface steering is crucial for engaging in a clean, uniform, and robust zinc coating. Without this step, the galvanizing way may additionally fail to offer the volume of protection desired for agency and business programs. Proper training devices the foundation for the following steps, making sure the fulfillment of the entire way.
Immersion in Molten Zinc
After floor education, the metallic is ready for the center step of the galvanizing technique: immersion in molten zinc. This is in which the protecting coating is performed. The metal is dipped into a tub of molten zinc heated to approximately 450°C (842°F).
During this immersion, a metallurgical reaction takes location a few of the metallic and the zinc, forming a chain of zinc-iron alloy layers. These layers are tightly bonded to the metal surface, developing a long-lasting protective barrier. The coating thickness relies upon on elements that incorporate the composition of the metallic, the time spent in the zinc tub, and the temperature of the molten zinc.
This step is critical in galvanizing as it offers the metal with its corrosion-resistant homes. The zinc coating serves as a physical guard in opposition to environmental elements which encompass moisture and air. Additionally, zinc has sacrificial residences, because of this it’s going to corrode in the location of the underlying metallic, providing introduced protection.
Immersion in molten zinc not only enhances the steel’s resistance to rust however moreover will also boost its ultra-modern durability. This step ensures that the protected metallic can resist harsh situations, making it best for use in manufacturing, transportation, and infrastructure tasks.
Cooling and Solidification
Once the metal is eliminated from the molten zinc tub, it undergoes cooling and solidification. This step is essential in galvanizing to ensure that the zinc coating units nicely and the office works a strong defensive layer.
As the blanketed metal is uncovered to air or water, the zinc solidifies, developing a hard, durable end. Cooling is generally completed hastily to save you any deformation or uneven coating. The manner also lets in the zinc-iron alloy layers shaped all through immersion to stabilize, ensuring the coating’s integrity.
This step is critical for accomplishing the popular mechanical houses of the galvanizing metal. It guarantees that the coating adheres firmly to the ground, providing an easy and uniform give-up. A properly cooled and solidified coating is a lot much less likely to crack, peel, or flake, even below mechanical stress or environmental exposure.
Proper cooling also enhances the classy attraction of the galvanizing steel, as it gets rid of irregularities or blemishes inside the coating. This makes the metallic not only practical but also visually appealing, this is specifically important for programs in which look topics, at the aspect of architectural duties or purchaser objects.
Inspection and Quality Control
Inspection and exquisite control are vital steps within the galvanizing way to make sure that the coating meets enterprise requirements and purchaser requirements. This involves an intensive examination of the galvanized steel to come across any defects or inconsistencies inside the coating.
Visual inspection is the number one technique used to evaluate the pleasantness of the coating. Experts take a look at for issues collectively with uneven thickness, bare spots, or excessive buildup of zinc. These defects can compromise the protecting houses of the coating and ought to be addressed earlier than the steel is allowed for use.
In addition to seen tests, specialized tests are completed to determine the thickness and adhesion of the zinc coating. Devices that consist of coating thickness gauges are used to make certain that the layer meets the preferred specs. Adhesion checks are accomplished to verify that the zinc coating is firmly bonded to the metal floor, making certain prolonged-lasting safety.
This step now not simplest guarantees the notable of the very last product but furthermore facilitates keeping the credibility of the galvanizing system. By adhering to strict wonderful manipulation standards, manufacturers can supply merchandise that is carried out reliably in actual-worldwide packages, whether or not in harsh commercial environments or normal use.
Final Finishing
The remaining step in a galvanizing manner is the very last completion, which incorporates getting ready the coated steel for its supposed use. This step complements the capability and appearance of the galvanized product, ensuring it meets specific application necessities.
Final finishing frequently includes duties that encompass removing any greater zinc or sharp edges that can have shaped the machine. This is accomplished to beautify the safety and cost of the metallic. For example, sharp edges can pose a threat at some point in dealing with or set up and ought to be smoothed out.
In some times, greater remedies are finished to beautify the coating’s houses. For example, a passivation layer may be added to enhance resistance to white rust, a not unusual trouble with newly galvanized steel. Alternatively, portray or powder coating may be implemented over the zinc layer to acquire a specific aesthetic or greater layer of protection.
Completion ensures that the galvanized metallic is ready for fast use or addition processing. This step now not only enhances the product’s usability but also offers price via tailoring the steel to fulfill the ideal desires of every challenge. It completes the galvanizing technique, turning in a brilliant, long-lasting product that is prepared to face up to the traumatic conditions of its surroundings.